14
0
0
Clogging Issues in Mini Asphalt Plant Pipelines
Clogging in mini asphalt plant pipelines is a common concern that can disrupt production and lead to costly downtime. Understanding the causes of these issues and implementing preventive measures is crucial for maintaining efficient operations. This article explores the commonality of clogging in mini asphalt plant pipelines and offers practical solutions to mitigate these problems.
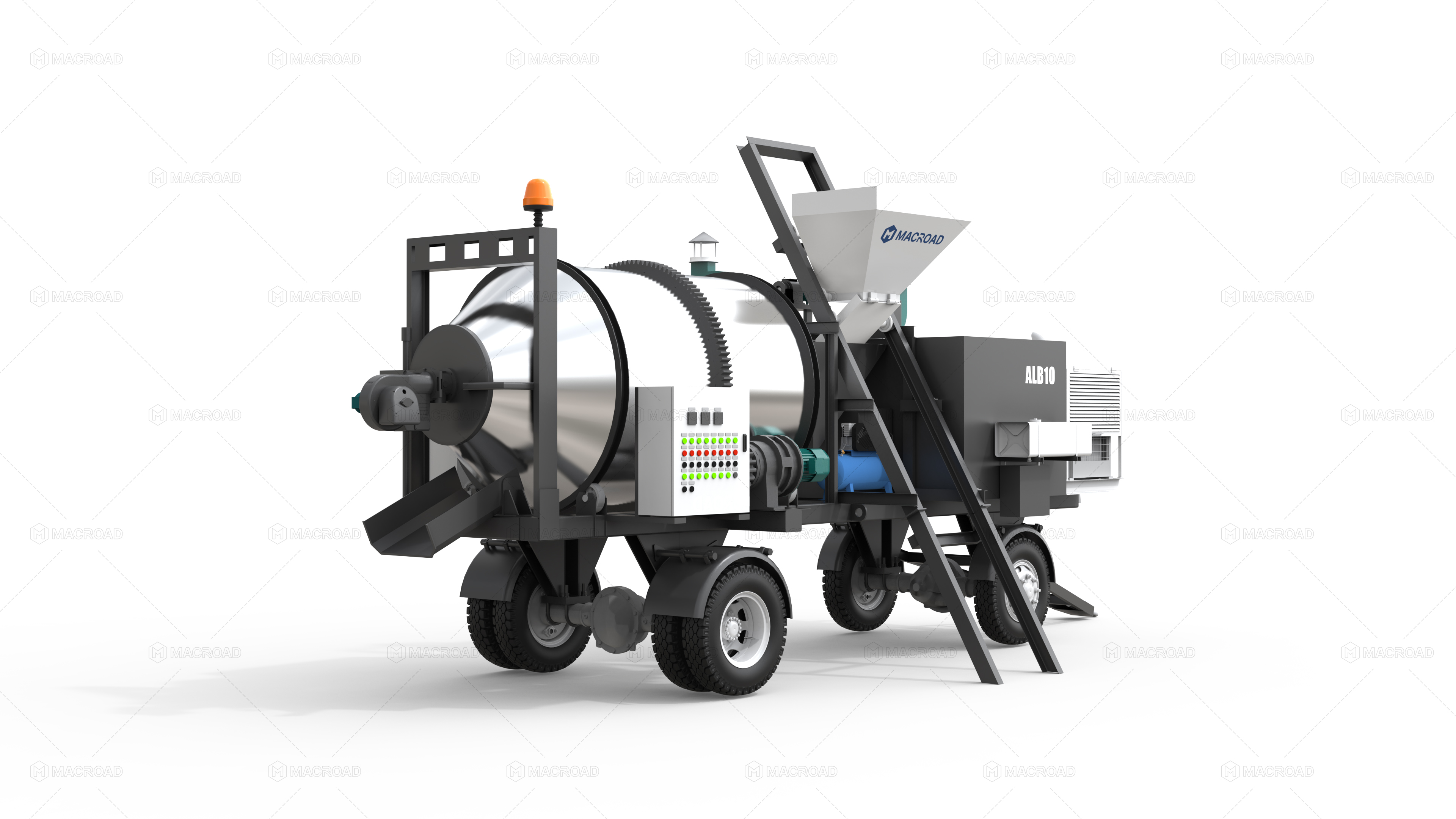
Understanding Clogging Causes
Clogging in mini asphalt plants often arises from a combination of factors, including the quality of materials used, temperature fluctuations, and inadequate maintenance. When aggregates and bitumen are not properly mixed or if the materials contain excess moisture, the likelihood of buildup increases. This accumulation can create blockages in the pipelines, hindering the flow of asphalt and affecting overall productivity.
Additionally, temperature variations can exacerbate clogging issues. Asphalt must be maintained at specific temperatures to ensure proper flow through the pipelines. If the temperature drops too low, the viscosity of the asphalt increases, making it more prone to sticking and causing blockages. Operators should monitor the temperature closely, especially in cooler climates or during nighttime operations.
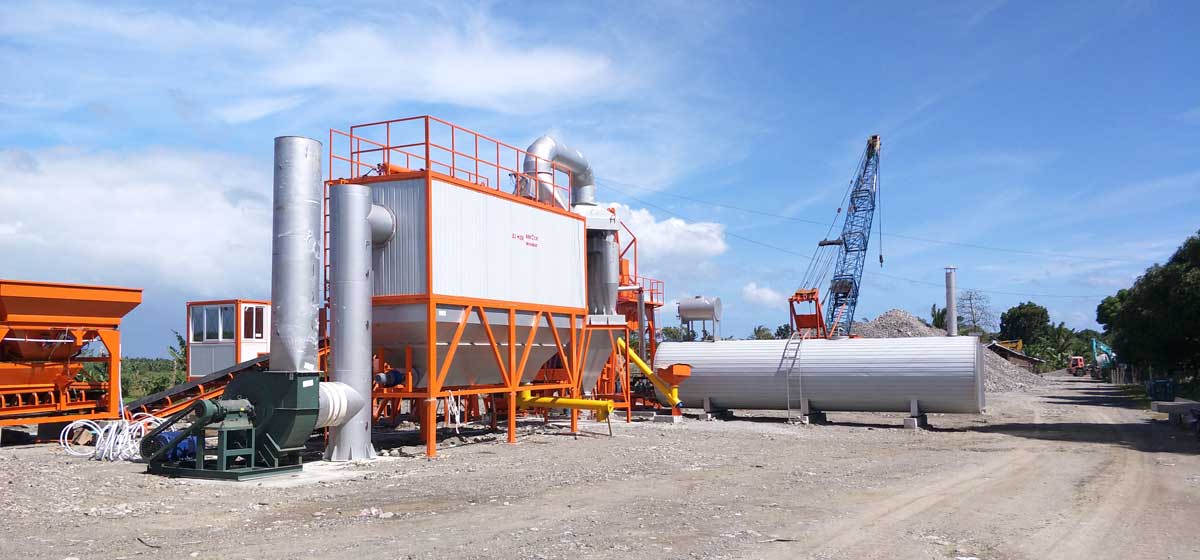
Preventive Measures for Clogging
To prevent clogging in mini asphalt plant pipelines, several proactive measures can be implemented. First and foremost, maintaining optimal material quality is essential. Using well-graded aggregates and ensuring that all materials are dry can significantly reduce the risk of clogs. Regularly inspecting the quality of the materials before they enter the plant can help identify potential issues early.
Another effective strategy is to maintain consistent temperatures throughout the production process. Operators should utilize heating systems to keep asphalt at the appropriate temperature, especially during colder months. Implementing insulation on pipelines can also help retain heat, ensuring that the asphalt remains fluid and less prone to clogging.
Regular maintenance is crucial for preventing pipeline clogs. Operators should establish a routine inspection schedule to check for signs of buildup within the pipelines. Cleaning the pipelines periodically, either through flushing with hot oil or using specialized cleaning tools, can help remove any accumulations before they lead to significant problems. This proactive approach not only reduces the risk of clogs but also extends the lifespan of the equipment.
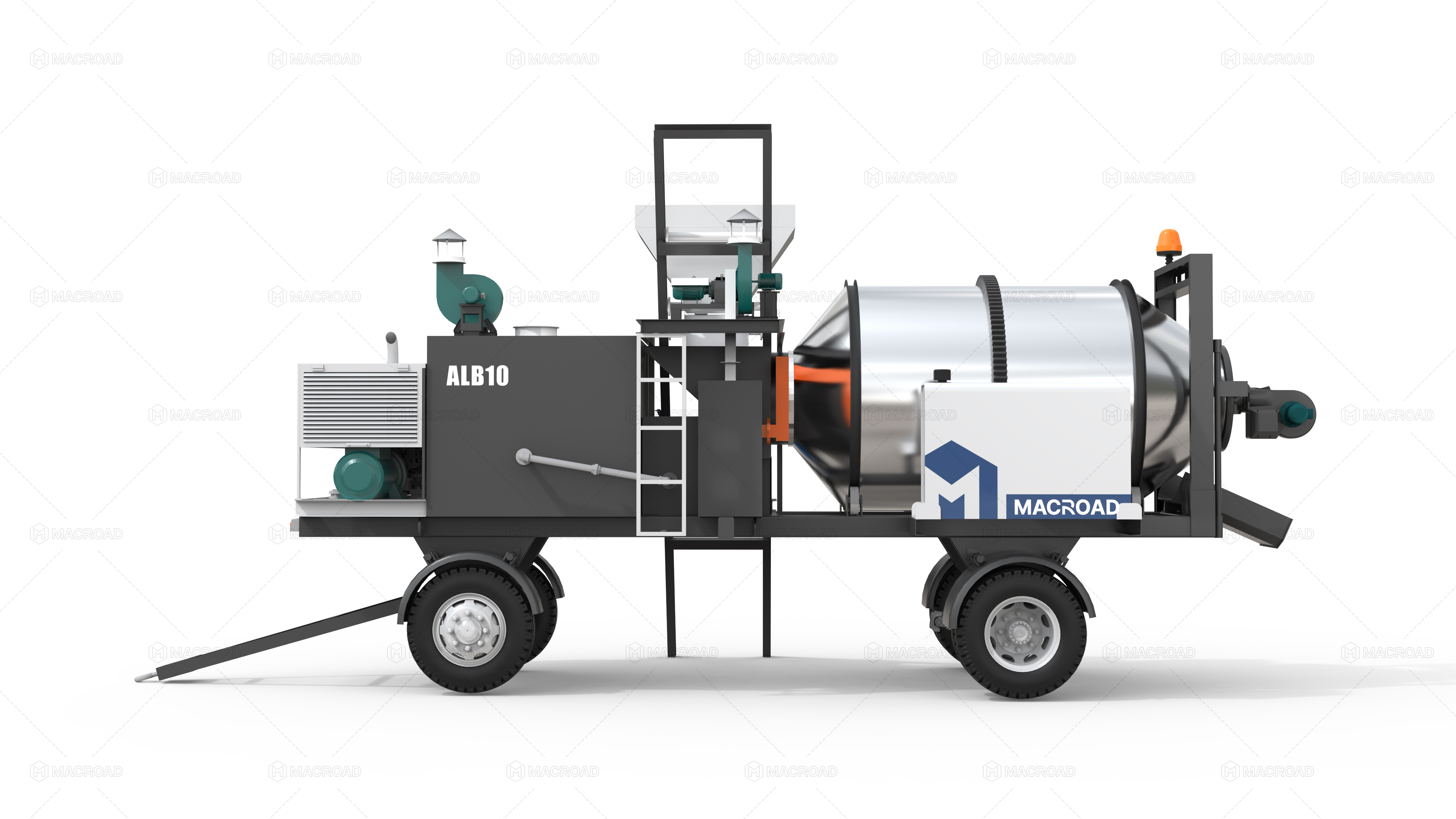
The Role of Technology in Prevention
Advancements in technology have also provided new tools to help prevent clogging in mini asphalt plants. For instance, modern plants often come equipped with automated monitoring systems that track temperature and flow rates in real time. These systems can alert operators to potential issues before they escalate, allowing for timely interventions.
Additionally, employing smart mixing technologies can enhance the uniformity of asphalt blends, reducing the likelihood of material inconsistencies that contribute to clogging. By ensuring that all components are mixed thoroughly, operators can minimize the risk of aggregate segregation or moisture retention, both of which can lead to blockages.
Training operators on best practices for preventing clogging is equally important. Ensuring that staff are well-versed in the operational parameters of the mini asphalt plant can help them identify and address potential issues proactively. Encouraging a culture of awareness and vigilance around pipeline maintenance can greatly improve overall efficiency.
Conclusion
In conclusion, clogging issues are indeed common in mini asphalt plant pipelines, but they can be effectively managed through careful attention to material quality, temperature control, and regular maintenance. By implementing preventive measures and leveraging technology, operators can mitigate the risks associated with clogs, ensuring smoother operations and minimizing downtime. Maintaining a proactive approach to pipeline management not only enhances productivity but also contributes to the longevity of the asphalt plant, making it a wise investment for contractors.
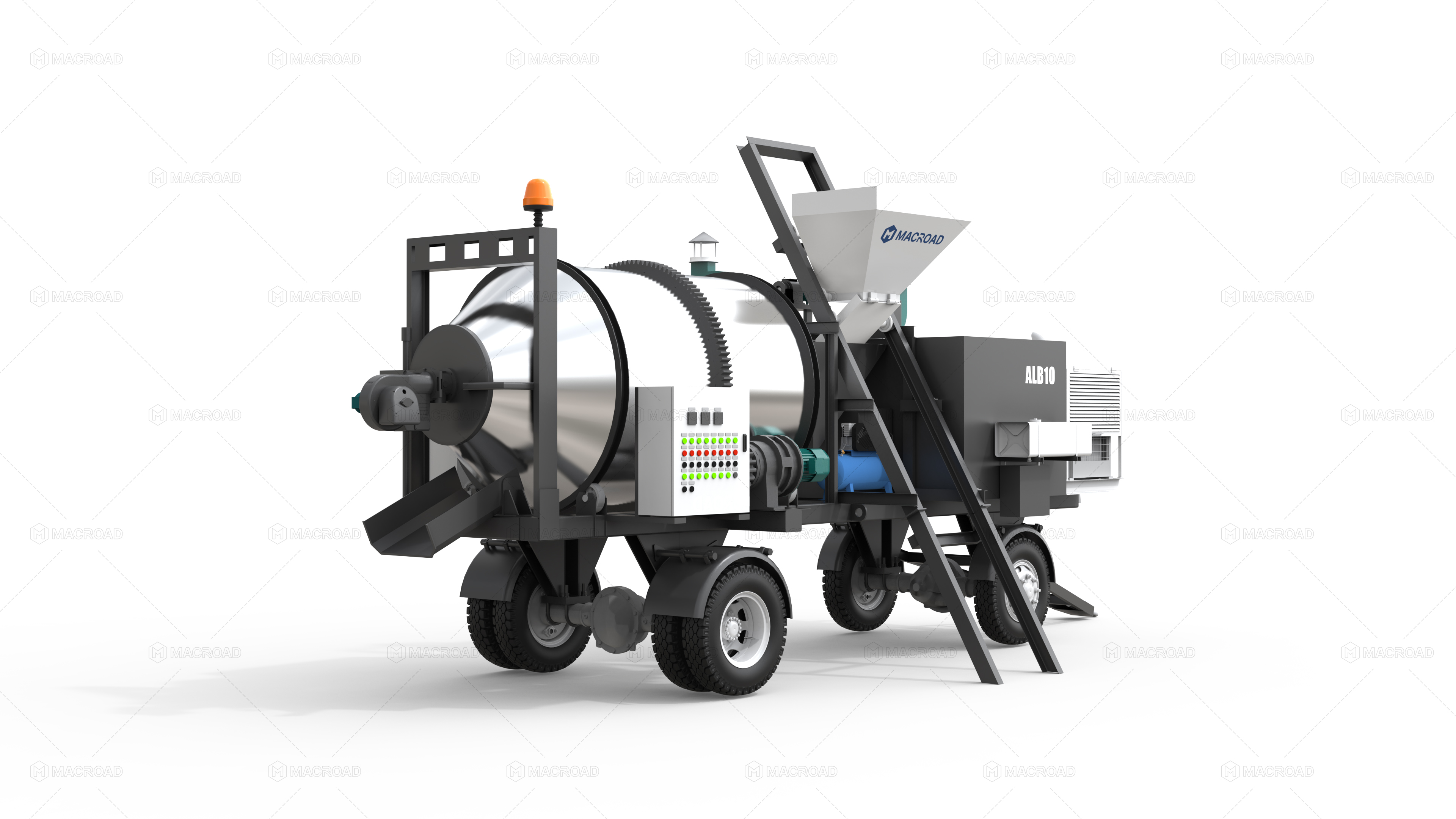
Understanding Clogging Causes
Clogging in mini asphalt plants often arises from a combination of factors, including the quality of materials used, temperature fluctuations, and inadequate maintenance. When aggregates and bitumen are not properly mixed or if the materials contain excess moisture, the likelihood of buildup increases. This accumulation can create blockages in the pipelines, hindering the flow of asphalt and affecting overall productivity.
Additionally, temperature variations can exacerbate clogging issues. Asphalt must be maintained at specific temperatures to ensure proper flow through the pipelines. If the temperature drops too low, the viscosity of the asphalt increases, making it more prone to sticking and causing blockages. Operators should monitor the temperature closely, especially in cooler climates or during nighttime operations.
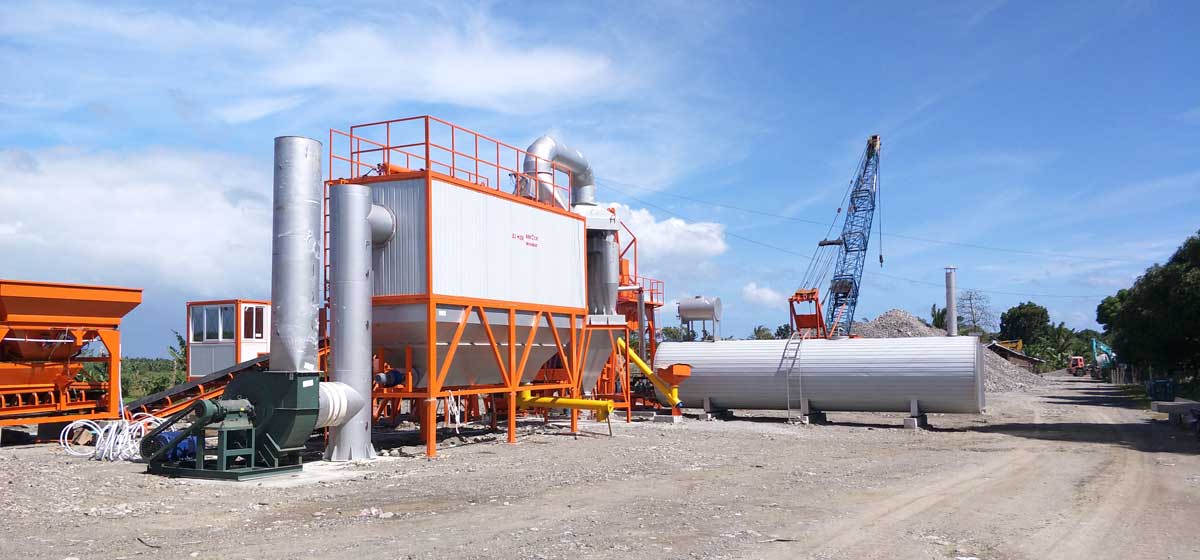
Preventive Measures for Clogging
To prevent clogging in mini asphalt plant pipelines, several proactive measures can be implemented. First and foremost, maintaining optimal material quality is essential. Using well-graded aggregates and ensuring that all materials are dry can significantly reduce the risk of clogs. Regularly inspecting the quality of the materials before they enter the plant can help identify potential issues early.
Another effective strategy is to maintain consistent temperatures throughout the production process. Operators should utilize heating systems to keep asphalt at the appropriate temperature, especially during colder months. Implementing insulation on pipelines can also help retain heat, ensuring that the asphalt remains fluid and less prone to clogging.
Regular maintenance is crucial for preventing pipeline clogs. Operators should establish a routine inspection schedule to check for signs of buildup within the pipelines. Cleaning the pipelines periodically, either through flushing with hot oil or using specialized cleaning tools, can help remove any accumulations before they lead to significant problems. This proactive approach not only reduces the risk of clogs but also extends the lifespan of the equipment.
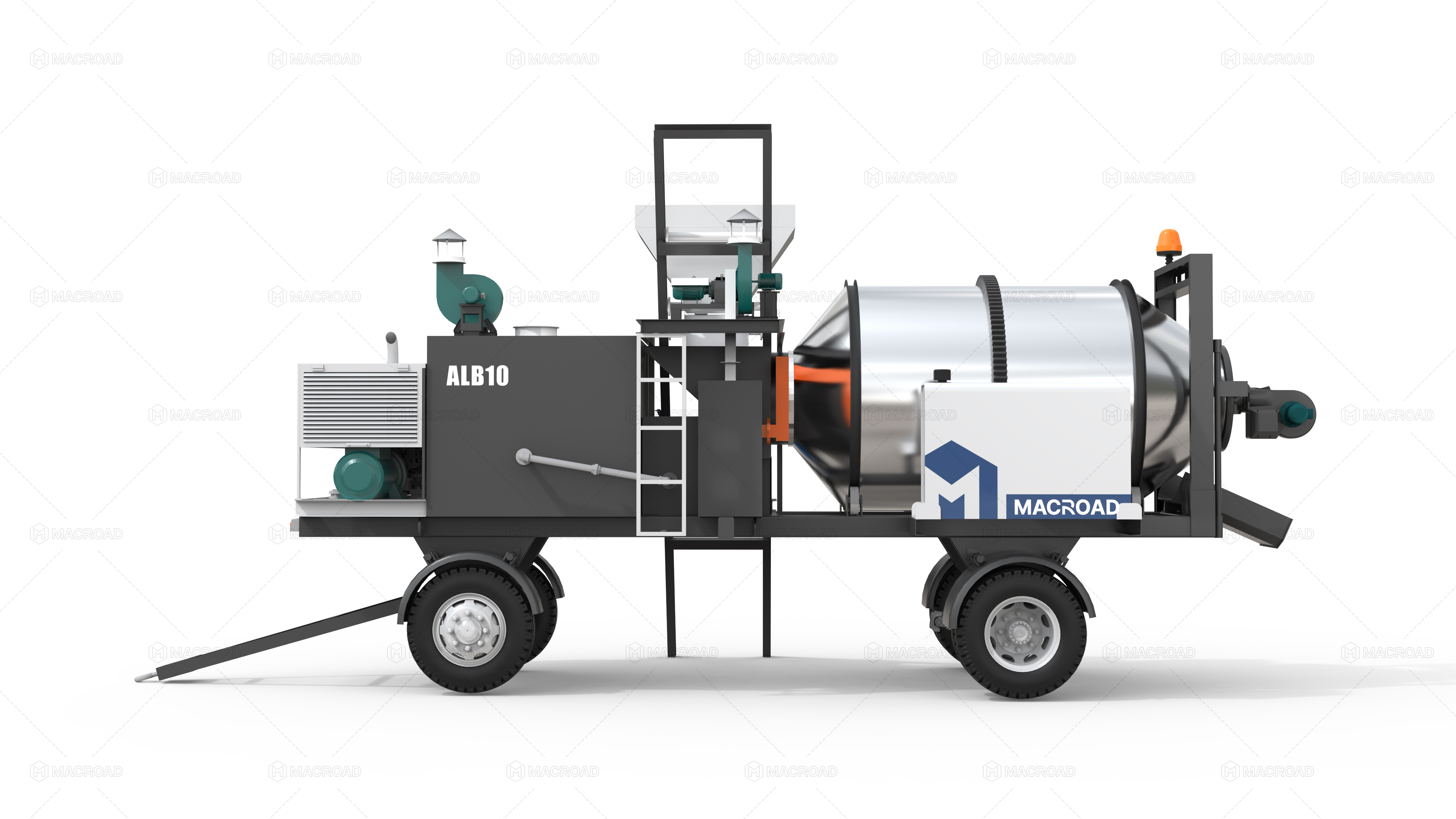
The Role of Technology in Prevention
Advancements in technology have also provided new tools to help prevent clogging in mini asphalt plants. For instance, modern plants often come equipped with automated monitoring systems that track temperature and flow rates in real time. These systems can alert operators to potential issues before they escalate, allowing for timely interventions.
Additionally, employing smart mixing technologies can enhance the uniformity of asphalt blends, reducing the likelihood of material inconsistencies that contribute to clogging. By ensuring that all components are mixed thoroughly, operators can minimize the risk of aggregate segregation or moisture retention, both of which can lead to blockages.
Training operators on best practices for preventing clogging is equally important. Ensuring that staff are well-versed in the operational parameters of the mini asphalt plant can help them identify and address potential issues proactively. Encouraging a culture of awareness and vigilance around pipeline maintenance can greatly improve overall efficiency.
Conclusion
In conclusion, clogging issues are indeed common in mini asphalt plant pipelines, but they can be effectively managed through careful attention to material quality, temperature control, and regular maintenance. By implementing preventive measures and leveraging technology, operators can mitigate the risks associated with clogs, ensuring smoother operations and minimizing downtime. Maintaining a proactive approach to pipeline management not only enhances productivity but also contributes to the longevity of the asphalt plant, making it a wise investment for contractors.
What is the function of mini asphalt plant
repair - 0 svar
road construction - 0 svar
Totalt 0 svar på denne avstemningen